Pilot Operated Pneumatic Stainless Steel Solenoid Valve Suppliers
Stockist of 2 Way Normally Open and Hydraulic Brass Solenoid Valves
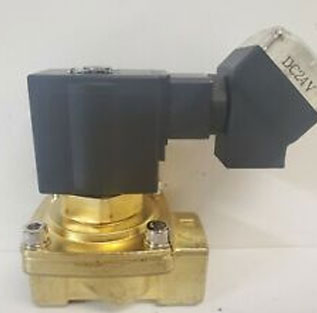
Solenoid Valve
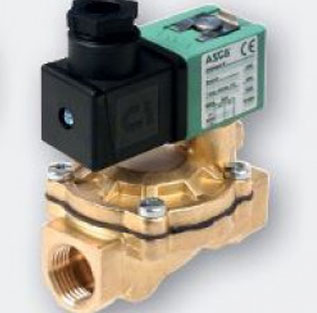
Pilot-operated Solenoid Valve
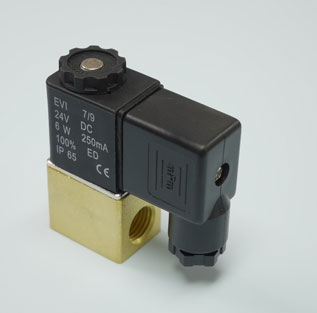
Two Way Solenoid Valve
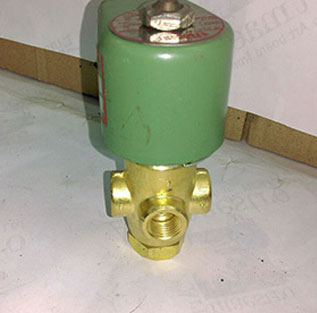
Three Way Solenoid Valve
Table of Content
Pilot-operated Solenoid Valve specification schedule
Specification | DN10 | DN15 | DN20 | DN25 | DN32 | DN40 | DN50 |
Application Liquid | Steam, water, air | ||||||
Operation Mode | leading format | ||||||
Type | Normally close | ||||||
Flow Aperture | 17 | 22 | 30 | 50 | |||
CV Value | 4.8 | 12 | 20 | 48 | |||
Thread Size | 3/8" | 1/2" | 3/4" | 1" | 1-1/4" | 1-1/2" | 2" |
Viscidity of Application Liquid | Under 20CST | ||||||
Pressure | Steam, heated air, oil 0.5-15kgf/cm² | ||||||
Maximum Pressure-reasistant | 0.2MPa | ||||||
Working temperature | -5~180℃ | ||||||
Application Voltage Range | +/-10% | ||||||
Body Material | Hpb59-1 | ||||||
Oil Seal Material | EPDM, PTFE | ||||||
Standard Voltage | AC:220V 110V DC:24V 12V |
Basic types of Two Way Solenoid Valve
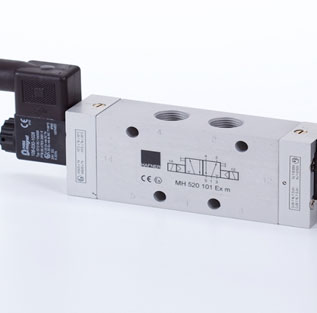
1/4 inch miniature bi-stable solenoid valve, 3.6 V pulse valves water
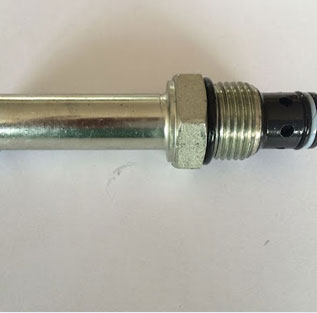
Steel Frame Solenoid Pull Push Type Electromagnetic Valves for Hydraulic
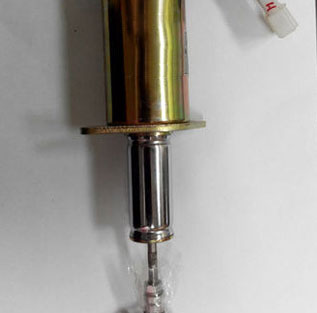
Solenoid valves 1503ES-12S5SUC11S stop solenoid
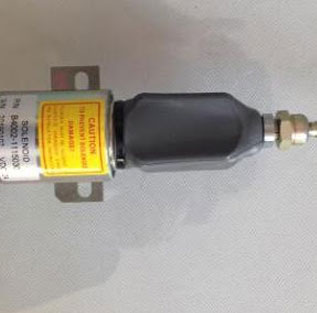
2/2 way 1/2 inch air water 24V stainless steel material solenoid valves
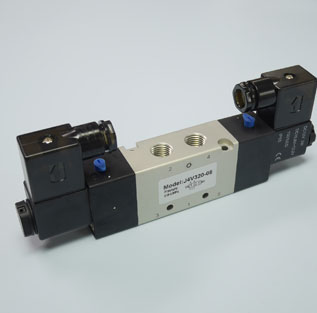
brass waterproof 3/4 inch Two-Way solenoid valves
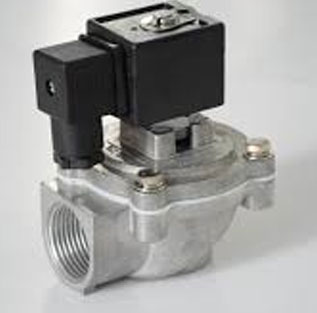
Electromagnetic Valve Dc Ac Pressure Relief Direct Acting Solenoid Valves
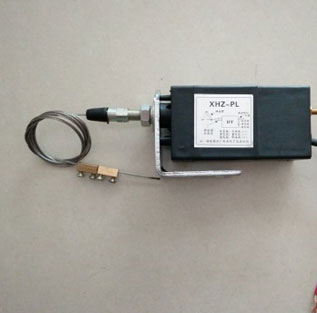
25Mm Stop Electromagnetic Valve Dc 24v Air Shutdown Solenoid Valves
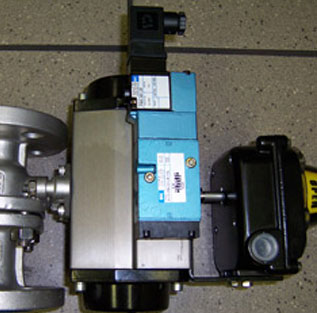
Dc 24v Pull Type Tubular Actuator Solenoid Valves, Stroke 10mm
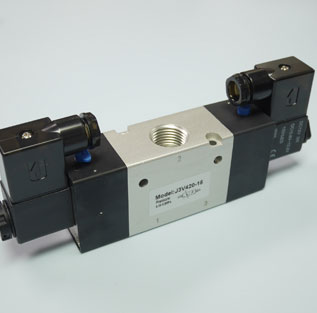
4V Series 4V410-15 Single Coil Big Size 1/2 inch Electric 5/2 Way Pneumatic Air Solenoid Valve Cylinder Valve
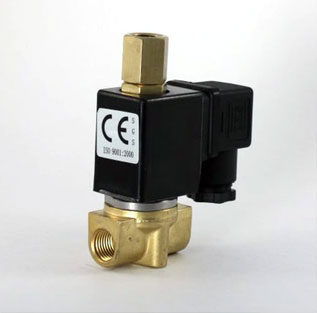
Ac 220v 380v Stroke 6mm 8mm Tubular Push Type Solenoid Valve for Electric Welder
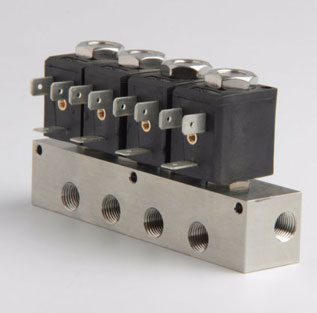
12v Solenoid Valve Air ride Suspension manifold valves SMV-01
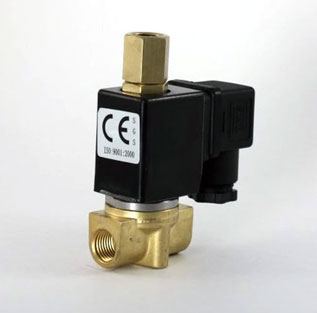
35A-AAA-DDAA-1BA DC24V MAC Three-Way Solenoid Valve
View Chemical Composition of Semi-Direct Operated and High Pressure Solenoid Valve in Stainless Steel and Brass
Chemical Resistance of Three Way Solenoid Valve
Material Code | Construction Material Chart | General Chemical Resistant |
---|---|---|
PA | Polyamide | Resistant to grease, weak bases, waxes, oils, fuels, alpatic and aromatic hydrocarbons. |
EP | Epoxy | Resistant to nearly all chemicals. Not resistant to low molecular organic acids in highly oxidising and high concentrations substances. |
1.4305, 1.4401, 1.4581 | Stainless Steel | Resistant to caustic and light acids solutions. |
PVC, PVC-HT | Polyvinyl Chloride (hard) | Resistant to caustic , most acids, and saline solutions. |
PP, PE | Polypropylene, Polyethylene | Resistant to many aqueous solutions of acids, organic solvents, bases and salts. |
PTFE | Polytetrafluorethylene | Resistant to nearly all chemicals. Not resistant to flurides & liquid sodium. |
PPS | Polythenylsulfide | Resistant to bases, aliphatic and aromatic hydrocarbons, aqueous mineral acids, many ketones, alchols, greases, water,halogenated hydrocarbons, oils and hydrolysis. |
PEEK | Polyetheretherketone | Resistant to most chemicals. Not resistant to concentrated sulphuric and nitric acid and certain halogenated hydrocarbons. |
PTFE* | Polytetrafluorethylene | Resistant to nearly all chemicals. Not resistant to liquid sodium and fluorides. |
EPDM | Ethylene Propylen Diene Rubber | Resistant to ozone and hot water. Not grease and oil resistant. |
FKM | Fluorocarbon Rubber | Resistant to oil and other chemicals, as well as heat. |
NBR | Nitrate Rubber | Resistant to oil. |
FFKM | Perfluorinated Elastomers | Resistant to weather, extreme heat and most chemicals. |
Varities of Solenoid Valves
- AC Laminated
- DC C–Frame
- DC D–Frame
- Linear
- Rotary
Check Latest Price List Of Proportional and Miniature Electromagnetic Valves
Prices of Pilot Operated Hydraulic Solenoid Valve
Solenoid Valves Prices | Three Way Solenoids Price list |
---|---|
JL900-Q1miniature solenoid valve |
$16.00-$48.00/ Piece |
Price List of 3 2 way 3 2 inch 110v 220v 24v brass waterproof high pressure pneumatic hydraulic air water solenoid valve | $4.90-$39.00/ Piece |
2W160-15 2 Way Normally Closed Solenoid Valve | $10.00-$11.00/ Piece |
electric power shut off screw normal opened brass body water solenoid valve | $27.00-$28.00/ Piece |
View PTFE, Tubular, 3 Port Diaphragm Type and ASCO 8210 Solenoid Valve Dimension
Pilot Actuated Solenoid Valve Dimensions Schedule
MODEL: 2S160-500 & 2W160-500 Series SOLENOID VALVE DIMENSIONS (MM) | ||||||||||
BRASS | STAINLESS STEEL | Port (NPT) | Cv | A | B | C | D | E | F | W (lb) |
2W160-10 | 2S160-10 | 3/8" | 4.8 | 101.5 | 57 | 117 | 69 | 36 | 56 | 1.6 |
2W160-15 | 2S160-15 | 1/2" | 4.8 | 101.5 | 57 | 117 | 69 | 36 | 56 | 1.8 |
2W200-20 | 2S200-20 | 3/4" | 7.6 | 107.0 | 57 | 124 | 73 | 36 | 56 | 1.8 |
2W250-25 | 2S250-25 | 1" | 12 | 111.5 | 74 | 135 | 99 | 36 | 56 | 3.2 |
2W350-35 | 2S350-35 | 1 1/4" | 24 | 142.0 | 95 | 172 | 123 | 63.5 | 66.5 | 5.7 |
2W400-40 | 2S400-40 | 1 1/2" | 29 | 142.0 | 95 | 172 | 123 | 63.5 | 66.5 | 5.7 |
2W500-50 | 2S500-50 | 2" | 48 | 172.0 | 123 | 209 | 168 | 63.5 | 66.5 | 9.9 |
Solenoid Valve vs Ball Valve
Solenoid Valves | Ball Valves |
|
|
3 Way Solenoid Valve Features
- Full bore design with fast response
- Small torque to On/Off,safety &reliability
- High platform structure with easy installation
- Bidirectional sealing & pressure enduring
- Fire proof apply with API607,GB/T6899
- Suitable for fiber ,particles and viscous media
Solenoid Valve Stockholder Of Following Manufacturers in UAE
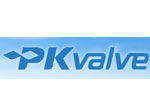
Stockist Of Solenoid Ball Valve in UAE
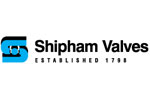
Stock Of Solenoid Butterfly Valve in Dubai
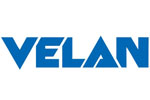
Stockist Of Solenoid Operated Butterfly Valve in Dubai
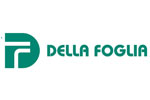
Supplier Of 2-way Solenoid Valve in Dubai
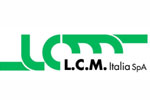
3-way Solenoid Valves Supplier in Dubai
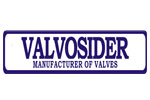
Stock Of Pneumatic Solenoid Valves in Dubai
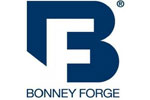
Spool Type Solenoid Valve Stockholder in UAE
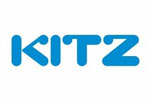
Normally Closed Solenoid Valve Stock in UAE
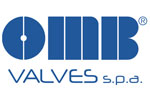
Normally Open Solenoid Valve Stockist in UAE
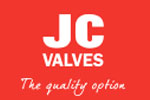
Stockholder Of Bistable Solenoid Valve in UAE
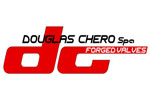
Supplier Of Water Solenoid Valve in UAE
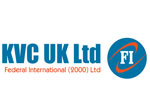
Low Pressure Solenoid Valve Normally Closed Stock in UAE
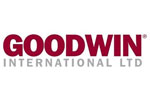
Solenoid Pilot Valve Stockist in Dubai
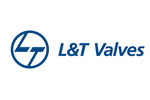
Stockholder Of Pneumatic Solenoid Valves in Dubai
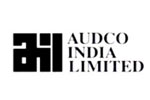
Hydraulic Solenoid Valves Stockholder in Dubai
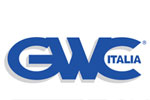
Solenoid Gate Valve Stocking Distributor in UAE
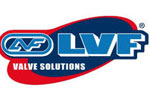
Stocking Distributor Stainless Steel Solenoid Valve in UAE
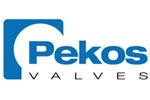
Stock Of Brass Solenoid Valve in UAE
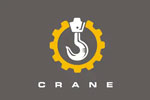
Miniature Solenoid Valve Supplier in UAE
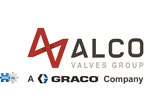
3/2 Solenoid Valves Stock in Dubai
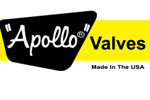
Stock Of Diaphragm Type Solenoid Valve in UAE
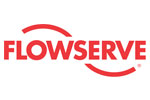
Safety Solenoid Valve Stocking Distributor in Dubai
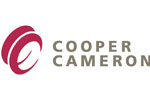
Stocking Distributor Of Poppet Type Solenoid Valve in Dubai